Picking the right sensor
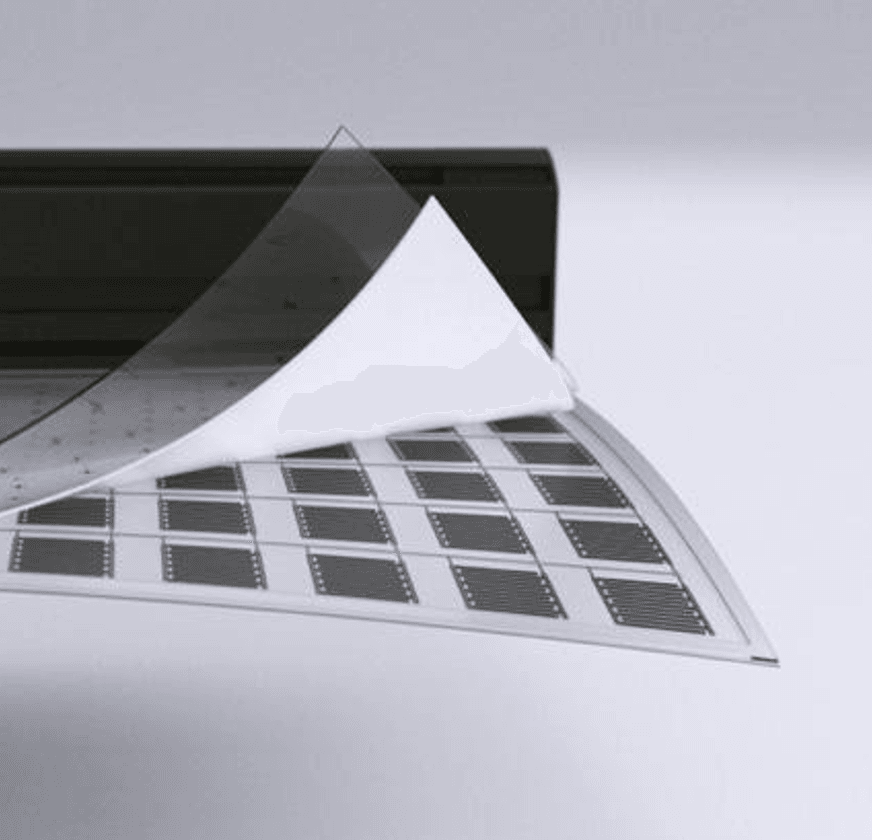
Is this the right shelf sensor? We'll find out
We often get questions from our clients about how to configure our sensors to their specific shelves or storage locations. These questions are not about the dimensions or customizations to get it to fit perfectly into a cabinet or cooler. Nor are they about the look and feel to fit the style guide, or about operating conditions and boundaries. All of these questions are perfectly fine and good for aligning expectations.
Where it begins to become tricky is when our clients start to sit in our seat. We've gained a huge amount of experience and learnings over the last couple of years in finding superior solutions to pick up signals across specific settings for various client use-cases. We have invested heavily in understanding the tech landscape, trade-offs, where we position ourselves, what you might be able to expect, and what is required to unlock various use-cases.
There's a ton of learning, some counter-intuitive findings, and a need for some discovery and tailoring, rather than upfront guidance. In any case, it requires guidance that we can navigate, and have learned to do better than pretty much any of our clients themselves.
In short, we can find the best solutions for you to pick up shelf signals. Let me explain.
It All Starts with a Superior Sensing Principle
How our tech stacks up against alternative sensor principles and creates an edge is quickly acknowledged. We have already discussed how the principle of sensing a surface is superior to visual image processing or product tagging (NFC, RFID). We have also discussed the limitations of traditional mechanical solutions (fixed form factor, limiting flexibility, intrusive, cumbersome) and printed matrix pressure sensors (expensive, limited response range, unreliable). Please see our blog 'Sensing Paper, Why?' for more background on how we play in a white space with our sensor tech.
Similarly, the whole notion that we correct a raw signal in our software layer and thereby correct all kinds of sources of distortion (temperature, humidity, drift, etc.) is also well understood. In the same fashion, our software layer that can recognize products and move to an ever-increasing range, precision, and edge-cases with increased data and ML training efforts is recognized. See 'Solve in Software'.
This puts us miles apart from any sensor or hardware vendor.
Reversed Logic: Min Spec vs Max Performance
Interestingly enough, the quest for the sensor set and signal processing is not a one-way path towards improving precision, accuracy, range, and reliability. In fact, we have discovered that in many cases 'good is good enough', avoiding gold-plated technology or wasted effort that over-spec a solution. The best example of this principle is in our solutions that simply warn you if you're running low. This is already possible with an indication of movement and some understanding of the speed of inventory movement. This does not require accurate count of products at all times, across the full operating range. If an operating procedure can be created that fixes a certain product to a location, then the need for product (type) recognition is relaxed. Minimizing specs can be a highly effective way to a better business case. It ensures that we start with the use-case and requirements and not a 'fix-all solution'.
The Trade-off Between Range & Resolution
Another question that we receive is about the trade-off between our solid, matrix sensor, or hybrid. Just as a recap:
- Our solid sensor basically has superior range, accuracy, and reliability, but only one single measurement for the complete sensor surface. This is great for a single product per storage location that can be stacked or piled, or in a container.
- Our matrix sensor has the ability to capture a heatmap of pressure points across a full surface area and thereby creates unparalleled flexibility to recognize different 'footprints' and accommodate different products. This works best with 'zoning' of products, i.e., assigning products to parts of sensor, like facings in a retail shelf. It provides the full flexibility to reshuffle zones and change them with a click of a button or (down the line) fully automatically.
- A hybrid combines one or multiple sensors in a combination. This can be a combination of solid and matrix sensors, achieving both benefits. Or a combination with other sensors, e.g., camera, switch, light sensor, movement sensor, to get additional information for additional accuracy.
The latter seems like an attractive way to solve anything, but naturally also adds additional cost. Like minimizing the requirements, the minimal solution set to hit and succeed these is just as important.
We don't determine this upfront.
Listen and Then Test & Learn
The way in which we find the perfect fit between requirements and the sensor solutions is partially determined up-front, but largely discovered and tailored to the specific client setting over time.
One of our clients was surprised to see us swap sensors. We were not replacing malfunctioning sensors, but actually changed the sensor set to a better fit-for-purpose. After a couple of months of operations and sufficient live feedback, we had gained a far better understanding of the signal requirements based on the current and roadmap of use-cases. In this case, the requirements for granularity of actual quantities proved to be more important in their operations than the need for flexibility in swapping or 'zoning products'. We therefore replaced the flexibility offered by our matrix sensor with a more reliable feed for stacked quantities from the solid sensor.
Similar examples actually occur in our software layer. We tailor our signal processing to the client needs over time. We can also learn from feedback with another data source (e.g., spot-checks or client feedback) or launch targeted software improvements for specific products or situations (e.g., product on the edge of a sensor). All of these improvements have a more continuous nature and can continue without any disruption of our client service.
In short, we can find the right combination of signal capturing and processing for your specific situation – and improve it over time.
Get in touch to assess how we can launch an initial solution for you and 'only get better'.