Complex Inventory Control
Dealing with Complex Inventory Control: Achieving Efficiency with MOOS
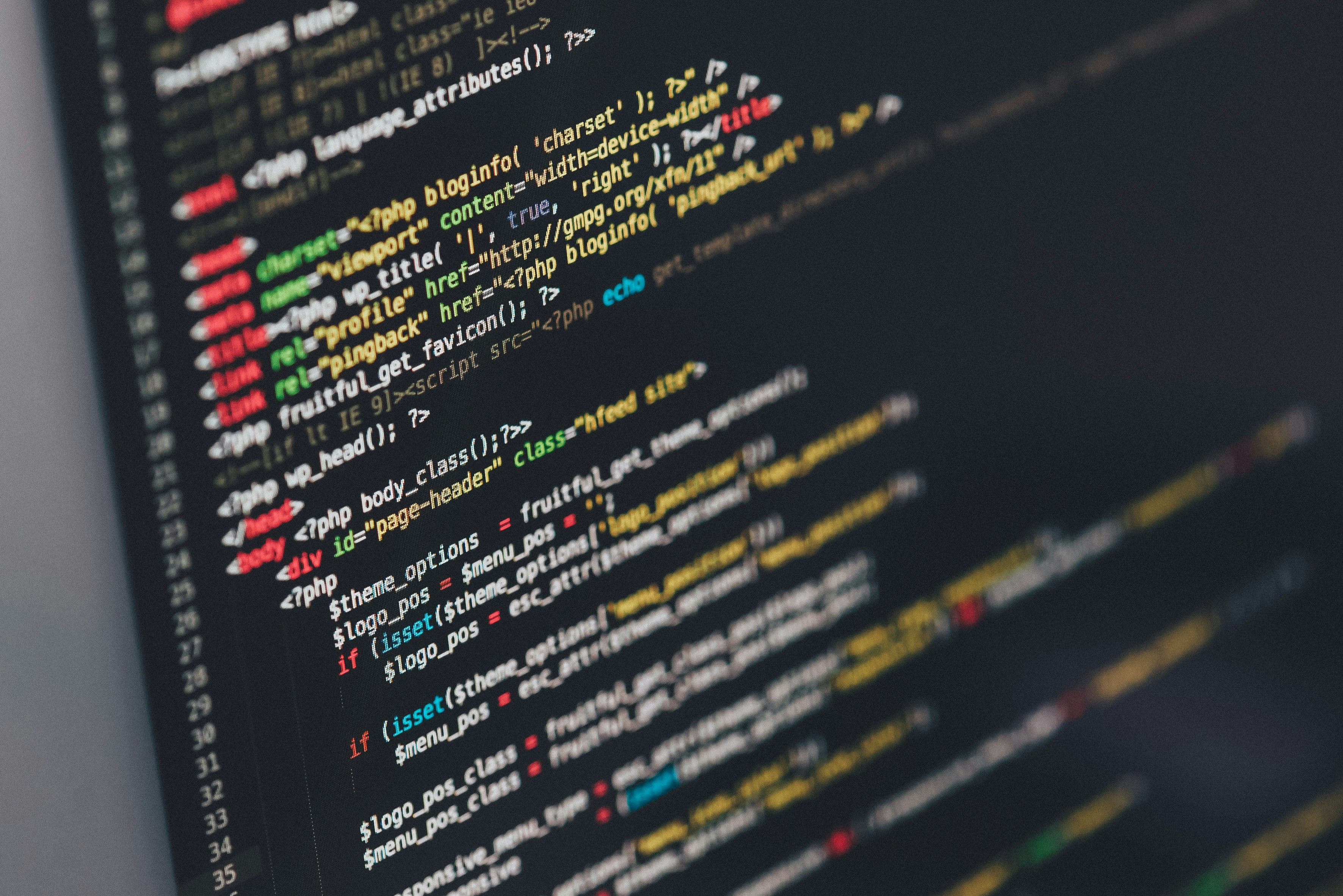
Dealing with complex inventory control
“How is it possible that we have tons of stock, a dedicated team to manage our inventory and still run out?” was one of the key questions that our client asked us. They really care about product availability, as the stock is critical to their operations and they have gone to great lengths to achieve this. They invested heavily in ‘intensive care’ operations, with processes, people, tooling to monitor and predict stock levels, and have invested even more in ‘safety stock’ to ensure that demand or supply variations are covered.
They are not alone. Many companies face similar challenges and see ‘control cost’ spiraling out of control and still experience disappointing service levels.
Tell-tail signs of challenged inventory control
Our client is an example of a ‘managed inventory’ situation, where ensuring product availability across multiple stock-keeping locations was outsourced to a dedicated party. They are responsible for the processes of re-ordering, replenishment, restocking and occasional counting and correcting. Their main KPI is stock availability at the point-of-use at acceptable cost levels (team, system, holding cost-of-inventory) and capex (storage locations and inventory management systems).
Our clients invested 10 weeks in measuring the stock levels (fill-rate) of approx. 100 product-storage locations. The results from this baseline measurement were shocking:
-
On average, the fill-rate never went below 50%, indicating a substantial ‘overstock’
-
There was a dedicated team that had daily check and replenishment actions for all 100 product-storage locations
-
Despite these buffers and special care, still, 20% of the product-storage combination ran out creating a shortage
Our client was alarmed by the level and started digging into the root-cases. It clearly became clear that the complexity of the inventory control problem was actually much higher than they anticipated. In fact, they realized that their current system, processes and people could not cope with the complexity.
Why is inventory control so hard to achieve?
Control cost can explode when the amount of different products, different demand patterns and different locations increases. Inventory control systems being challenged by some complexity drivers:
-
Criticality of the stock. High price, high rotation, high margin or high cost of running out, e.g. missed sale or missed production cycle and high ‘correction cost’, e.g. rush-orders, customer care actions
-
Demand predictability. Consistent demand and supply is obviously easy to manage. On the other hand, lumpy or intermitted demand or supply patterns, can easily create unexpected situations
-
Response system is challenged. If you can replenish your product quickly, cheaply and reliably, you probably don’t run into stock-out problems. If one or several of these are challenged, then the risk naturally increases.
-
Distributed control. Different SKUs that are required at distributed, independent locations multiplicate the control challenge. One central safety stock is a better natural buffer. Combined variance is lower than the sum of independent variance.
-
Constraints in storage space, capex or cash, ultimately creating a cap than can be lower than the required safety stock levels for a target availability level
-
Human error, spillage or shrinkage. Some product or processes simply have a higher risk profile. We’ve been surprised on several occasions at our clients that product can disappear mysteriously.
So, how did MOOS help?
The complexity of inventory control can be simplified dramatically with stock visibility.
The classic supply chain techniques like prediction, planning, processes and procedures are fine in many situations. However, once the complexity of your inventory control challenge increases, this quickly runs into limitations.
In such cases, the next performance bracket of higher availability levels at lower overall cost can be achieved by ‘seeing what is coming’. Visibility in the actual inventory movement at the point of use can make a world of difference.
Our client in the example mentioned above, put this into practice. They implemented the moos operating system with sensors in the storage locations and integration of the inventory insight in their operations. After a short period of integrating the additional insights into their day-to-day way of working, they immediately experienced the benefits of step-change in availability, literally making stock-outs part of the past.
In addition, over time, they learned how to adapt their operations and storage locations and could achieve lower overall average inventory levels, less replenishment actions, lower control cost, lower correction costs and lower capex.
Interested in achieving similar breakthrough in your inventory control?
Just get in touch. We are happy to explore how MOOS can help you in a similar way.