Availability Assurance
Live feeds of shelf/storage inventory can boost your availability assurance
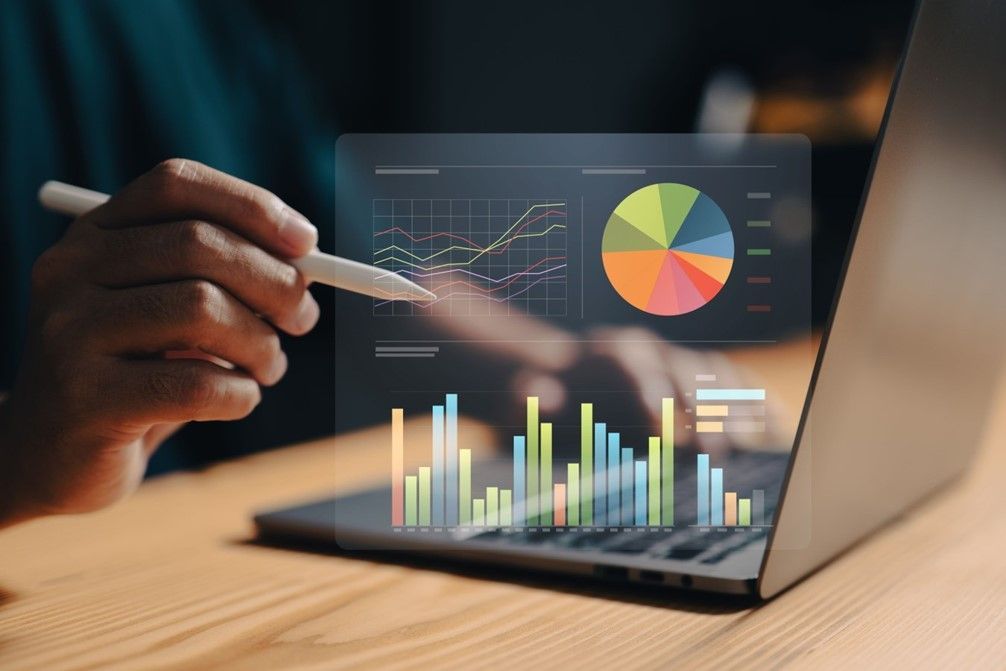
Ensuring availability? How simple solutions can drive superior results
Anybody running a store or operations knows the challenge of managing availability of their products. Order more than enough and you’re left with excess stock, order too little and you might run out and lose your sale or delay your production shift.
While the problem is clear, the solution is not. Over the past decades, tons of researchers, consultants and solution vendors have offered companies support to address this challenge. The recent surge in data science and AI have only added to the craze.
They typically follow a path of increasing sophistications towards solving supply availability. While helpful, they might ultimately defeat the purpose, adding more ‘control cost’ than the ‘cost avoidance’ they realize.
At MOOS, we’re increasingly finding that a simple solution beats sophisticated ones and we have a role to play when it matters most and predictability is challenged.
The availability challenge
The overarching objective of supply planning is getting the right products, at the right place, at the right time. Achieving this in a business setting requires striking a balance between inventory availability or service levels (e.g. on-shelf availability) and the overall system cost. This could consist of storage costs, transportation costs, control costs (e.g. labor for counting, correcting and ordering or IT systems like WMS) and, in more advanced calculations, cost-of-capital and asset utilization (e.g. FTL for transport).
In a steady-state predictable system, this is a fairly simple calculation to get the ‘economic order quantity’ (EOQ). The equation becomes a little bit more challenging when some constraints are introduced like batch or drop sizes, drop frequency, physical constraints (e.g. storage space), perishability, etc.
And, the challenge really starts when variance is introduced. For instance in demand or usage patterns, across lead-times, across production quality (e.g. defect rate) or introducing spillage risk (i.e. the euphemism for theft). Especially, when these are not straightforward, normal distributions, but irregular, intermitted or have a ‘fat long-tail’. The latter refers to low probability, high impact cases, e,g. complete supply disruptions or a whole delivery batch disappearing due to theft.
Integrating these type of challenges has been a feast for academics and a whole generation of data scientists, creating elegant supply management systems that can accommodate many real-life complexities.
Getting it right… most of the time
However, in practice, many companies do not have the ability, time and resources to study and control their supply problem. Business realities will simply direct them to simple heuristics, that have proven to work in many run-of-the-mill cases.
The most commonly used inventory control system is called ‘min-max’. Simply reorder when you hit the MIN inventory level and replenish till the MAX. It might take a bit of optimization or testing & learning to dial in the MIN and MAX levels, but once it’s set-up, it actually takes care of the complex equations in a fairly solid way. As long as the MIN covers an acceptable ‘safety stock’, that, in turn, covers a good deal of the deviations in demand and supply, then you’re good. It is also easy to automate and control.
The problem only starts to occur when ‘when it matters most’ and the ‘good availability’ is simply not good enough. The applies for products with an extremely high ‘penalty cost’. For instance, bottleneck products that, by themselves have limited nominal value, but are required for production cycle. Suddenly, the cost of non-availability shot up to the cost of a production delay. In many industrial settings, this can be insanely expensive and easily expressed in ‘millions per minute down time’. Just imagine the ‘aircraft-on-ground’ situation or a unanticipated site shut-down.
The typical management approach in such a case would be to keep an extremely high degree of redundancy and safety stock, e.g. Kanban systems with spares behind the WIP inventory. While this might work for a handful of products, it quickly breaks the bank of you need this for a broader range of items, slightly more expensive items or if you need items across dispersed locations.
Alternatively, companies introduce ´intensive care´, with people or systems checking-in more frequently. One of our clients, actually implements both and has a whole team dedicated to the task of ensuring that the safety stock doesn’t run out for critical bottleneck products. This is not only a very costly solution, it’s also ineffective beyond a certain point. Our client could have the weird situation of a huge surplus of nearly all bottleneck products and still run out of one of them that could stop the line.
So, what can you do? Isn´t there a better way?
Getting it right… when it matters most
Yes, there is a better. When you run into the limitations of what you can predict or the limitations of what you can reasonably keep as safety stock, there is a way to push beyond these boundaries. It’s actually painfully simple:
If you measure your inventory movement at the point of usage, you can use this to anticipate and prevent a stock-outs, rather than waiting till you’re too late. You just need the ability to see inventory movement as they occur at your stock-keeping location.
At MOOS, we’ve developed a proprietary system to capture the inventory movement on your shelf or storage locations. Integrating this into your inventory replenishment system can bring new levels of product assurance.
We have proven at our clients that using our system is far superior than pushing prediction models or control systems with safety stock into areas that they are simply not suited for. You cannot predict what is inherently unpredictable. Somebody stealing a batch, a misplacement, a failure, unprecedented peak in demand, etc.
Whenever you need real product assurance, MOOS is here to help.